Stopped Shipments, Stalled Profits:
Unplanned Downtime in Logistics
Understand the risks, financial impact, and strategies to keep your supply chain moving.
Unplanned downtime from logistics failures isn’t just a temporary setback—it’s a major financial and operational risk. Production halts, missed deliveries, and skyrocketing recovery costs put pressure on businesses to rethink their approach.
To stay competitive, companies need solutions that not only address challenges but also prevent them from escalating. But how can you minimize disruptions before they happen?
Here’s what we’ll cover
- Section 1: The True Cost of Unplanned Downtime
- Section 2: The Ripple Effect of Disruption
- Section 3: A Comprehensive Approach to Prevention
- Section 4: The Technology Solution for Reducing Unplanned Downtime
- Section 5: Key Takeaways
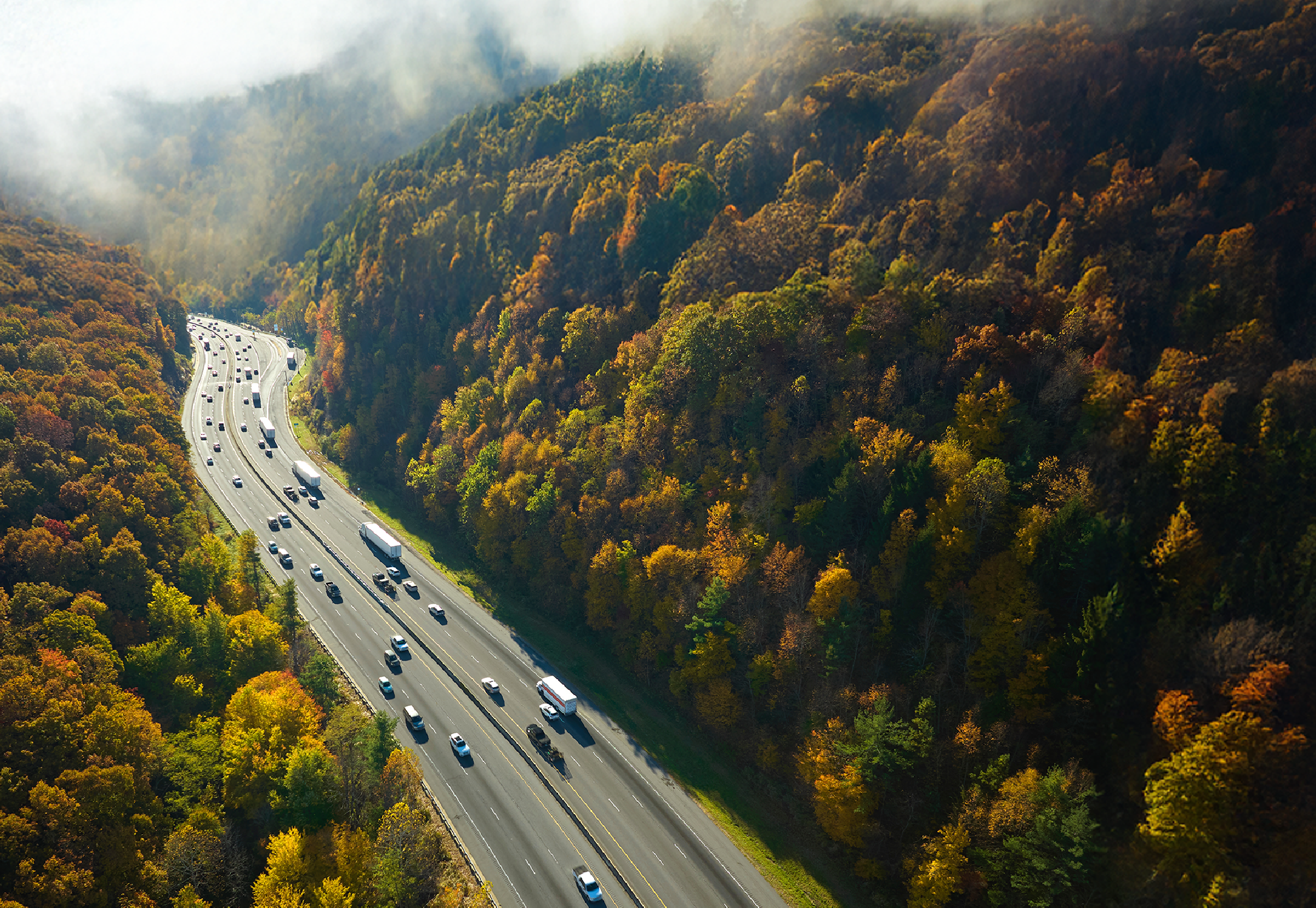
Section 1: The True Cost of Unplanned Downtime
Logistics-related disruptions can lead to significant financial losses, with companies losing hundreds of thousands of dollars each hour. Delays in crucial raw material shipments cause production lines to stop, impacting deadlines, increasing costs, and straining supplier relationships.
Recognizing these risks enables businesses to identify weak points and turn potential downtime into strategic opportunities for improvement.
Section 2: The Ripple Effect of Disruption
Production breaks not only derail schedules but also delay customer orders, complicate inventory management, and increase expediting costs.
Over time, these disruptions lead to strained supplier relationships and weakened market positioning, ultimately eroding both operational and financial efficiency.
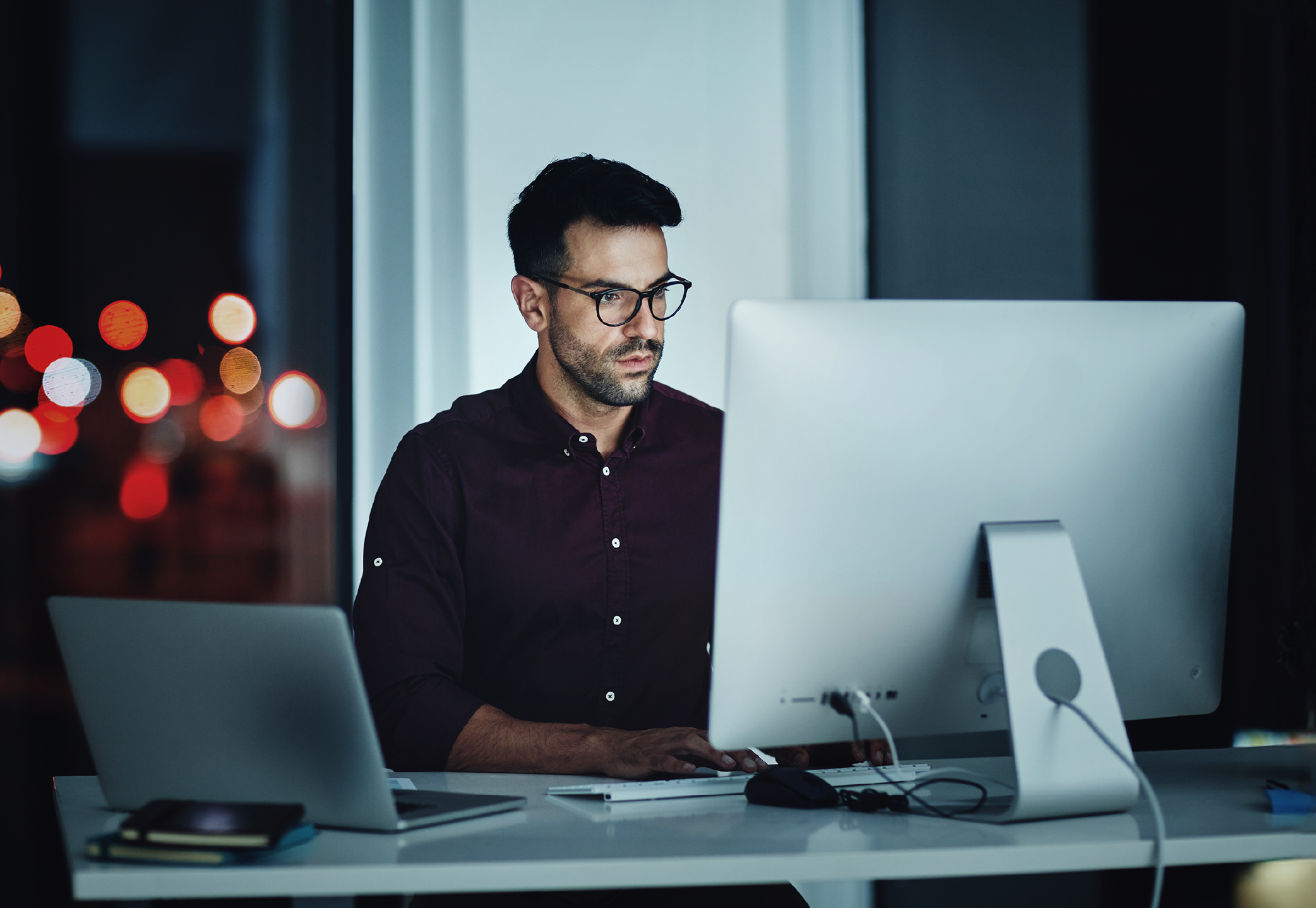
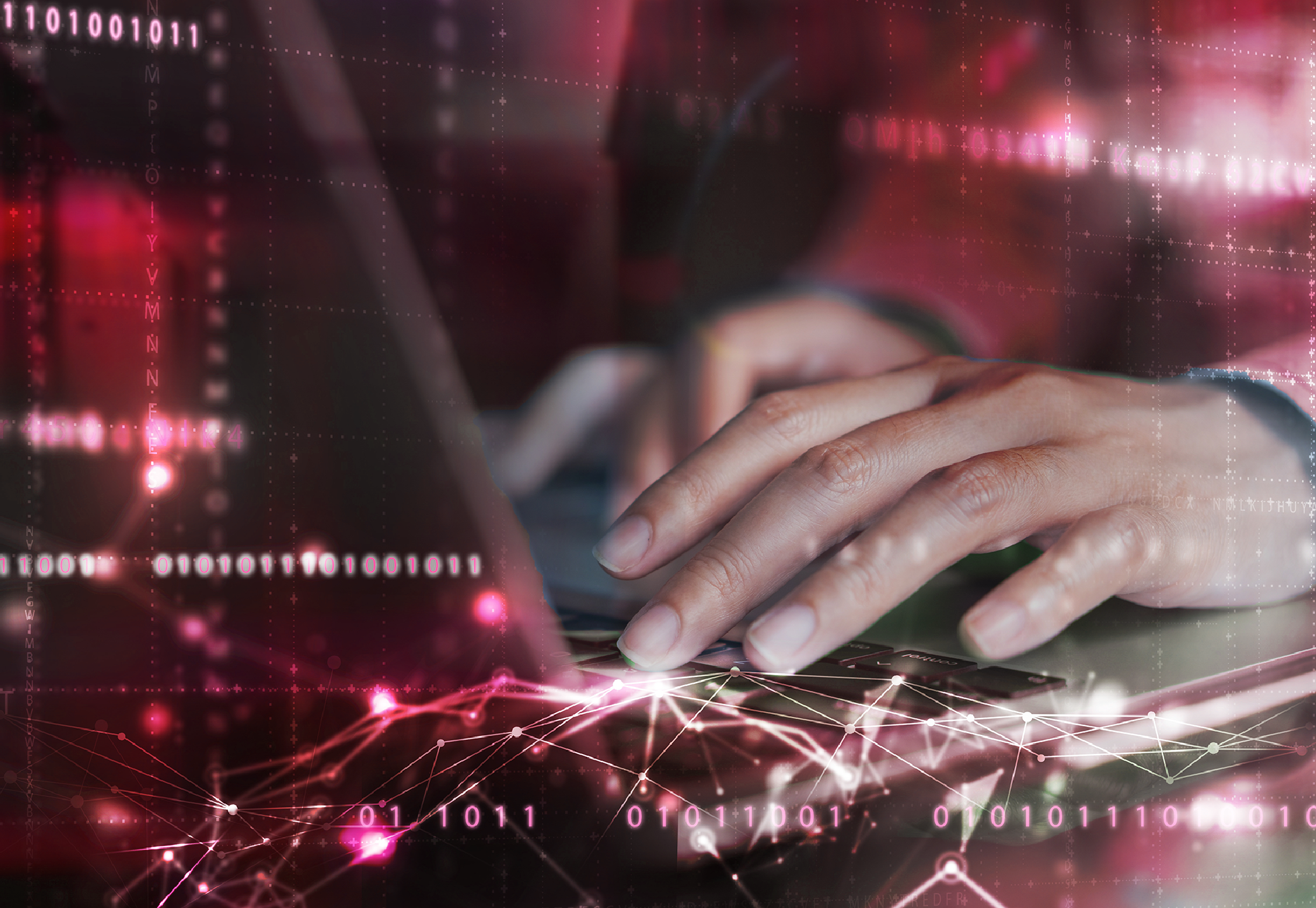
Section 3: A Comprehensive Approach to Prevention
A comprehensive approach to preventing logistics disruptions includes three core strategies: enhancing visibility through real-time tracking and inventory monitoring, proactive monitoring using predictive technologies and early warning systems, and strategic communication with strong reporting systems and carrier protocols.
These methods empower businesses to identify and mitigate potential disruptions before they cause significant operational damage.
Section 4: The Technology Solution for Reducing Unplanned Downtime
A Transportation Management System (TMS) minimizes unplanned downtime through features like real-time tracking, route optimization, and predictive delay forecasting.
By implementing a TMS, companies can reduce downtime by up to 77%, cut costs, and improve operational efficiency.
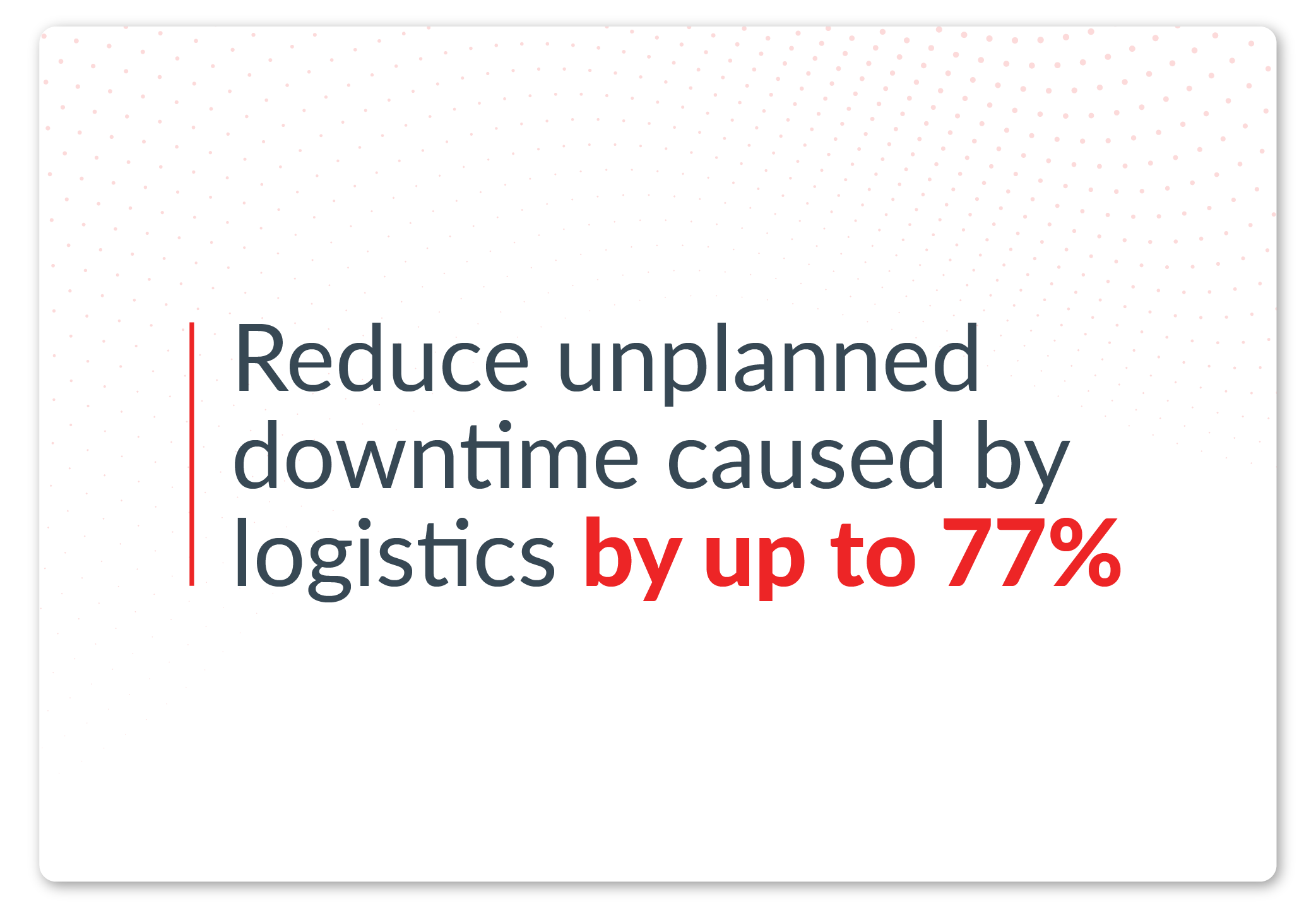
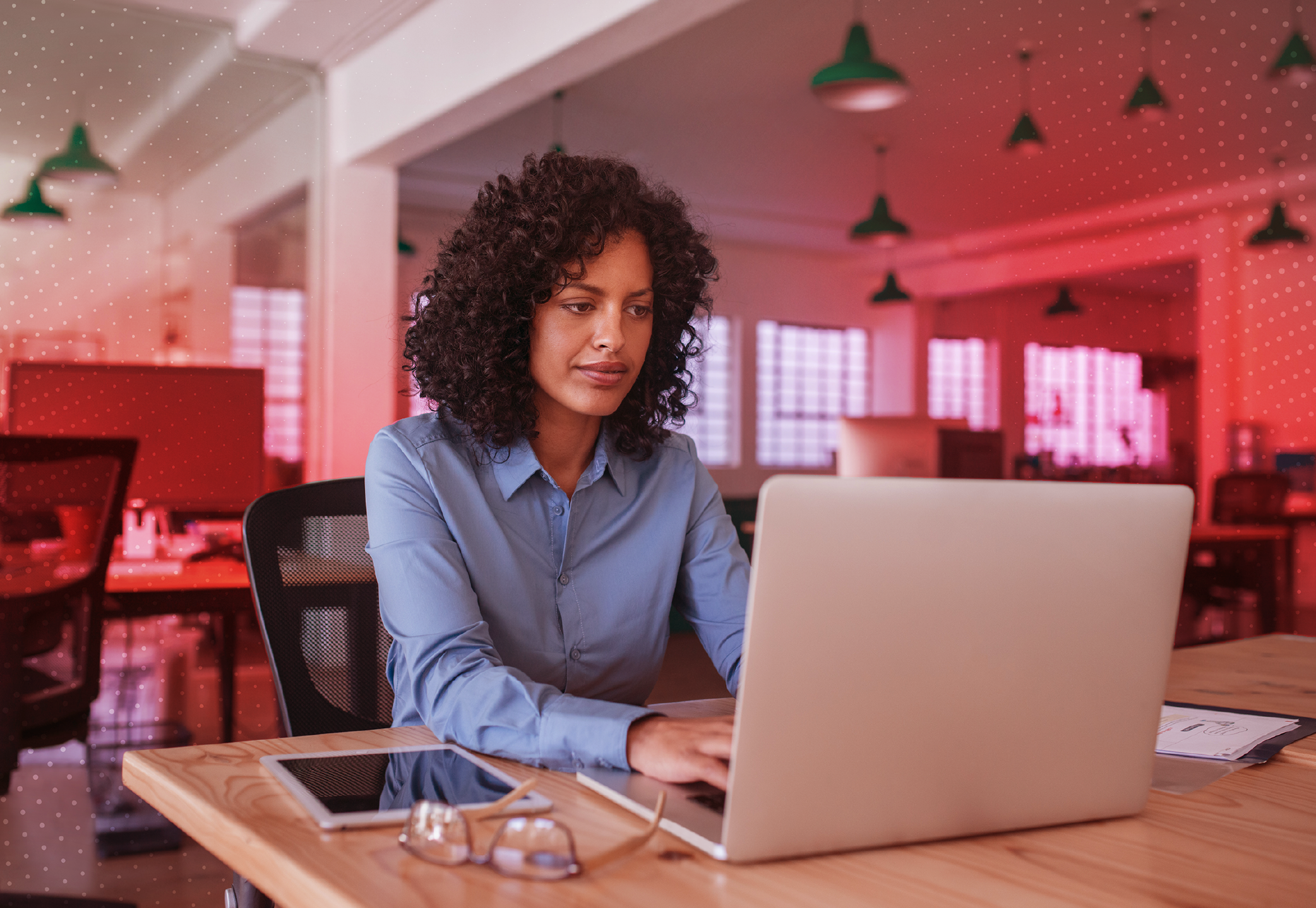
Section 5: Key Takeways
Unplanned downtime now impacts every aspect of a business, from manufacturing to supply chain logistics. By utilizing the right technologies and strategies, companies can shift from managing risks to gaining a competitive advantage.
Prevention, not reaction, is key to achieving cost savings and long-term operational strength.
Download the Full Report
Get ahead of disruptions and explore how advanced technology can improve your supply chain’s resilience.